板材零件滲碳淬火中出現(xiàn)的問題及改進(jìn)
板材是經(jīng)沖壓加工制造成形的零件,現(xiàn)已普遍應(yīng)用于工業(yè)縫紉機(jī)和汽車等行業(yè)中?紤]到其沖壓和加工性能,許多零件采用低碳鋼制造,通過滲碳淬火處理,提高零件的強(qiáng)度和耐磨性。我廠熱處理設(shè)備為UBE-200可控氣氛滲碳爐。在多年生產(chǎn)過程中,我們遇到一些零件在滲碳淬火中出現(xiàn)的問題,現(xiàn)總結(jié)如下:
(1)由于淬火油的低溫冷速不足造成SPCC材料零件滲碳表層出現(xiàn)馬氏體與屈氏體混合組織。
SPCC材料成分質(zhì)量分?jǐn)?shù)w(%)為:<0.12C,<0.50Mn,<0.040P,<0.045S。SPCC材料零件滲碳淬火后表面含碳量為0.85%左右,相當(dāng)于T8或T9鋼。其馬氏體轉(zhuǎn)變溫度為220℃左右。其滲碳淬火工藝為860℃×30min后滲碳80min(Cp為0.9%)后淬油。
我廠采用的淬火介質(zhì)為快速光亮淬火油,在更換整槽油后,發(fā)現(xiàn)SPCC材料零件強(qiáng)度和韌性嚴(yán)重降低,經(jīng)檢查發(fā)現(xiàn)滲碳表層組織為馬氏體與屈氏體混合組織。由于是換油后出現(xiàn)的,因此認(rèn)為是淬火油引起的。一般認(rèn)為,出現(xiàn)屈氏體是淬火冷卻速度不夠造成的,也就是說是由于淬火油中溫階段即蒸汽膜階段冷速較慢造成的。新油的冷卻曲線如圖1中曲線a所示,其中溫階段冷速能夠達(dá)到快速光亮淬火油國(guó)家標(biāo)準(zhǔn)要求。為此我們測(cè)定了舊油的冷卻曲線,如圖1中曲線b所示。經(jīng)比較發(fā)現(xiàn),兩油的低溫冷速相差很多,特別是300℃以下,相差更大,因此我們認(rèn)為造成滲碳混合組織的原因是淬火油低溫冷速不夠。為此我們調(diào)整了新油的低溫冷速,調(diào)整后的冷卻曲線如圖1中曲線c所示,用調(diào)整后淬火油處理SPCC零件,滲碳淬火組織正常。
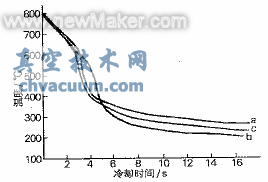
圖1 淬火油冷卻曲線
a.新油b.舊油c.調(diào)整后
因此我們認(rèn)為,淬火油的低溫冷速對(duì)具有相同的滲層碳濃度分布淬火件的組織有較大的影響,適當(dāng)?shù)靥岣叽慊鹩偷牡蜏乩渌,能夠增加零件的淬火硬化層深,改善淬火組織,提高零件強(qiáng)度。
(2)由于零件表面脫碳造成的反常組織。
由板材制造的零件,其表面一般不加工或只進(jìn)行磨削加工,而且加工量很少。因此假如板材表面脫碳,在加工過程中脫碳層一般不會(huì)去掉,這樣滲碳淬火中就可能出現(xiàn)反常組織。
我們處理過SCM415零件,其材料成分質(zhì)量分?jǐn)?shù)w%為:0.13~0.18C,0.15~0.35Si,0.60~0.85Mn,<0.030P,<0.030S,0.90~1.20Cr,0.15~0.35Mo。其滲碳淬火工藝為860℃均熱30min后滲碳60min(Cp為0.8%)后直接淬油。滲碳淬火硬化層深為0.3mm。零件只經(jīng)過一道磨光工序。在滲碳淬火后檢查發(fā)現(xiàn),由表面向心部金相組織依次為馬氏體+碳化物,鐵素體+珠光體+馬氏體,板條馬氏體,即在滲碳層后出現(xiàn)了鐵素體+珠光體+馬氏體的反常組織。檢查原始零件,發(fā)現(xiàn)零件表面嚴(yán)重脫碳,脫碳層深達(dá)到0.4mm,因而在滲碳過程中,脫碳層沒有被全部滲上,在隨后的淬火中出現(xiàn)了反常組織。我們認(rèn)為,板材表面脫碳層深只要不超過滲碳層深的一半,對(duì)滲碳沒有太大的影響,但對(duì)較深的表面脫碳層必須引起注意,以防出現(xiàn)反常組織,降低零件使用壽命。
(3)由于零件裝爐方式不當(dāng)造成零件局部軟點(diǎn)
我們處理的2mm厚的薄壁件,要求滲碳淬火后表面硬度為(700±70)HV。原采用碼放7層的方式裝爐,滲碳淬火后,發(fā)現(xiàn)零件有局部軟點(diǎn),最低硬度為420HV。由于所用設(shè)備的淬火油槽的冷卻攪攔裝置,使油的流向是由下向上,因此零件碼放7層后,阻擋了油的流動(dòng),造成油槽內(nèi)局部的油靜止不流動(dòng),使零件造成局部硬度軟點(diǎn)。
因此,將零件改成吊掛裝爐方法,保持油的流動(dòng)通暢。為減少變型,設(shè)計(jì)專門的吊掛夾具,使零件垂直向下入油,零件淬火后硬度均勻性良好,滿足了用戶要求,得到用戶好評(píng)。